
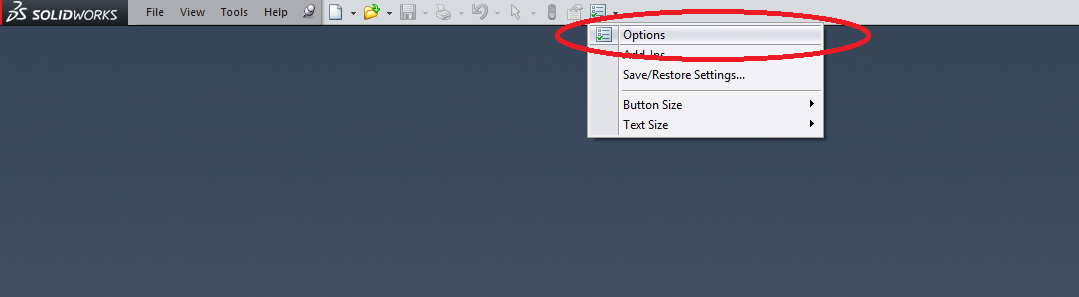
An Excel spreadsheet layout of a standard steel sheet metal gauge table.įigure 5. The tables will need to be formatted in the following layout:įigure 4. We are now going to create three different tables in Excel, each one representing a different material.
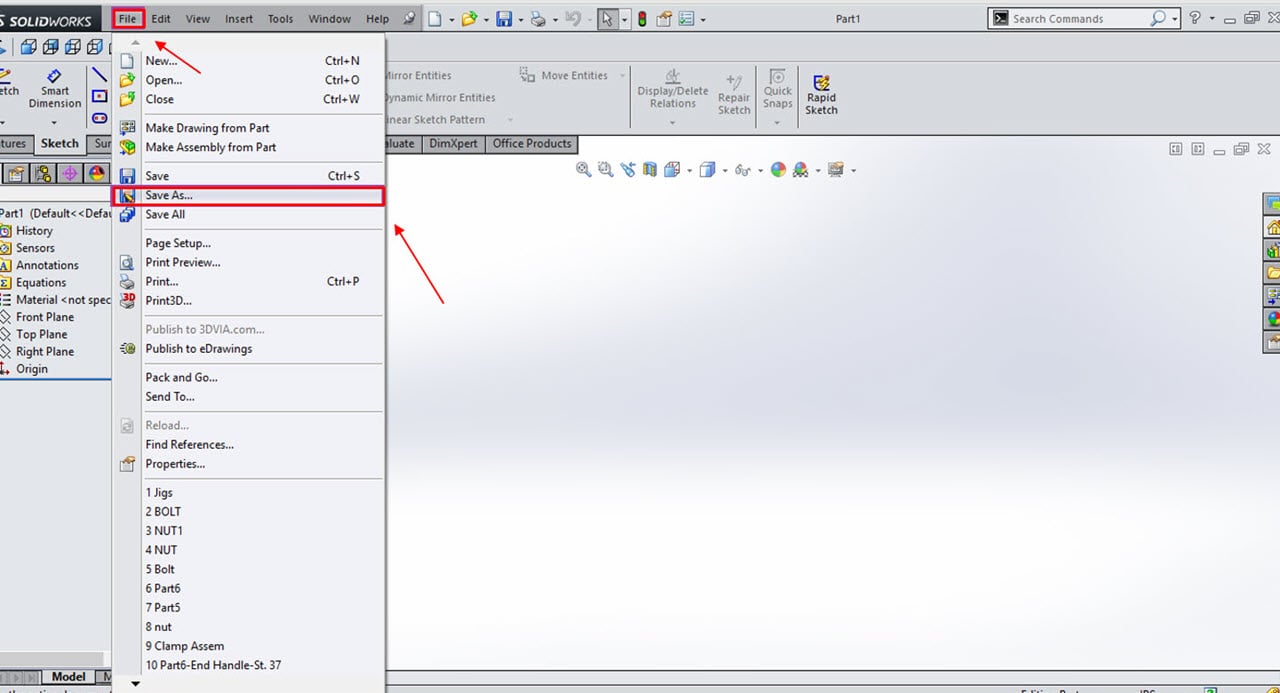
Without a sheet metal gauge table in SOLIDWORKS, whenever we create a sheet metal model, we would have to reference this table and manually type the values into SOLIDWORKS. In Figure 3, we can see a table that might be present in a sheet metal shop. A table of different materials, gauge thicknesses and default radii. Lastly, users can specify the appropriate K-factor to represent the stretch of the sheet metal in the bent corners.įor today’s example, we will create three sheet metal gauge tables representing the following materials and gauge values:įigure 3. Users can also specify the available default bend radius based on available tooling. Sheet Metal Gauge TablesĪ great tool available to SOLIDWORKS sheet metal users is the “Sheet Metal Gauge Table.” In this table, users can configure a Microsoft Excel spreadsheet to represent the appropriate sheet metal wall thickness, based on material and gauge values. Instead, we will simplify this area of the blog by agreeing to work with a K-factor value of 0.5. We could spend an entire blog describing the various options/techniques used in calculating the appropriate value to represent the stretching of sheet metal in bend regions. The third and final question that a SOLIDWORKS designer working with sheet metal will have is “How is the metal stretching/deforming in the bend region?” The phenomenon of sheet metal stretching in the bend region is often referred to as “bend deduction” or “bend allowance.” There are many techniques available to calculate what the “bend deduction” or “bend allowance” should be in these bend regions, but one of the most versatile is known as K-factor. Regardless of the bending method, a question that will often be asked by the designer is “What bend radius should I be using?” The answer to this question will be based on the thickness of the sheet metal and the available tooling being used in the bending process. This technique (known as bottom bending) is just one of many methods available to create a bend radius in a sheet metal design. The punch and V-die will each have a radius at their peak, and these radii will cause a specific bend radius to be formed in the sheet metal.

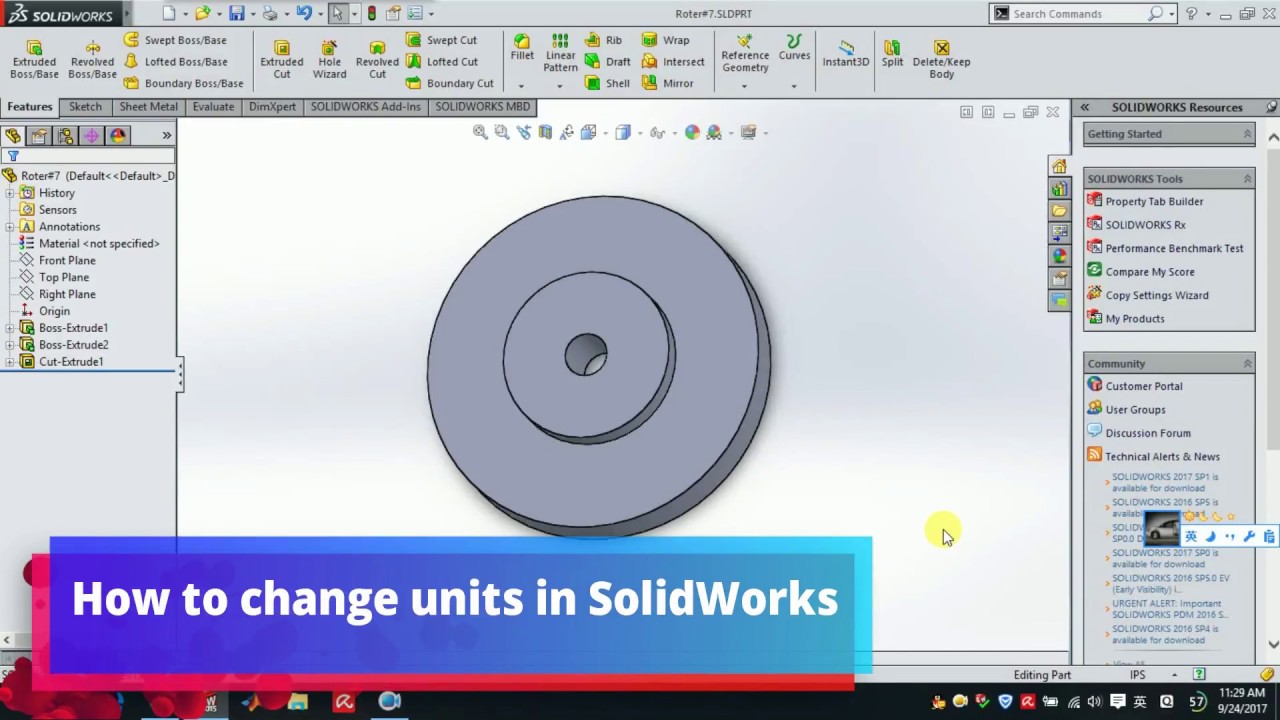
The flat sheet metal would be positioned between the punch and the V-die, and the press would be forced closed, forming a bend in the sheet metal. The V-die would be mounted on the lower part of the press, and the punch would be mounted on the upper part of the press. This punch and die set would be mounted in a press. A section view of a typical punch and die set used to create sheet metal bends.įigure 2 shows us a typical punch and die set used to bend sheet metal. The bend radius of a sheet metal design will be based on the wall thickness of the part and the tooling that is available in house.įigure 2. The second important number when creating sheet metal designs is the bend radius value. These differences can be hard to keep track of, and mistakes can occur when looking up the value and manually typing this value into SOLIDWORKS. This wall thickness will be different, depending on the material being used. Īs we can see in Figure 1, the gauge value number will be translated to a specific wall thickness. An example of a reference table for looking up sheet metal thickness based on gauge size and material. But what do these gauge values translate to, in terms of sheet metal wall thickness? In order to answer this question, we often need to look up the values in a table.įigure 1. We often see the specification for sheet metal wall thickness represented as a gauge value. The bend allowance/bend deduction of the sheet metal (specified in K-factor)īy configuring and utilizing a sheet metal gauge table, we can speed up the process of selecting the correct wall thickness (based on gauge value) and selecting the correct bend radius (based on available tooling).We can also automate the process of selecting the appropriate K-factor.When working in SOLIDWORKS to create sheet metal designs, we will often need to know three important values:
